The True Cost of Embodied Carbon
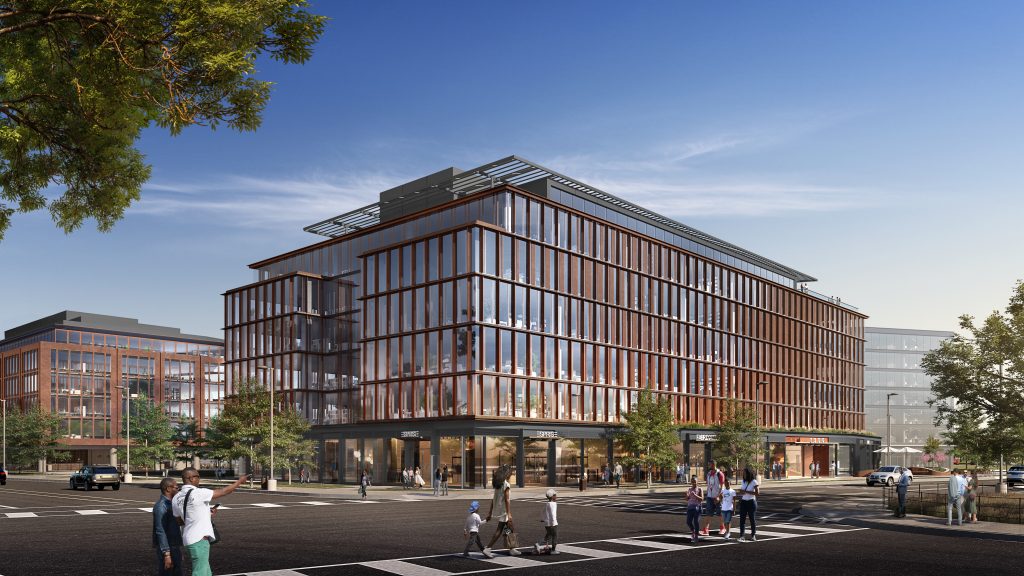
In 2021, Hickok Cole, Redbrick LMD, Arup, and DPR Construction were awarded a Building Innovation Grant from the Department of Energy and Environment to study the Lifecycle Analysis of Embodied Carbon for 1300 Sycamore Drive at St. Elizabeths Campus.
Having recently delivered their report, we asked Design Director Elba Morales and Senior Project Architect Kerron Miller to share further insights on their findings and why grant opportunities like these are vital to driving what’s next in design.

Tell us about the value of grant programs when it comes to advancing adoption of high performance design strategies. Why did we pursue the Department of Energy and Environment’s (DOEE) Building Innovation Design Assistance grant?
We have a responsibility to seek out and test strategies to lessen the impact of our buildings on the environment. Some of these tools and methodologies may be newer to market or have yet to be applied early on to certain project typologies. These DOEE grants give us the opportunity and resources to study key areas of interest like energy performance or embodied carbon on real projects in ways beyond what we normally do for current project work. Throughout the process, we report back to the DOEE and receive feedback which provides valuable insight to both parties. There’s also a deliverable component so what we discover has a potential impact on future projects and research. We don’t design in a vacuum. The more depth of knowledge we have, the better our buildings are now and in the future.
How did you choose your area of study? What were you hoping to achieve by analyzing sources of embodied carbon?
Embodied carbon is a particularly important topic for our industry because it considers the lifecycle of a building and its components. It tells us how much greenhouse gases are released into the atmosphere and how a specific project—and the material choices we make—contribute to global warming. However, it’s not something we typically assess during early stages of design, when decisions about the primary structure and envelope matter most. It’s generally assumed that low embodied carbon materials would come with a high premium, but we wanted to explore that idea further, and formulate a methodology to test alternative materials early on and evaluate cost in a broader conversation with our engineers, the owner, and the general contractor.

What made 1300 Sycamore at St. Elizabeth’s Campus a good candidate to study?
The biggest factor in any project is to partner with a client whose goals align with yours. We were interested in pursuing this grant idea and our client Redbrick LMD was on board. They want to build projects with greater longevity and higher long-term value, which made our partnership ideal. The other important detail here is that this particular site is not constrained by surface area, which is super rare in DC. Our constraints were height and overall density which meant we could consider an alternative model with a larger floorplate and taller ceiling heights with cross laminated timber, without losing overall square footage.
How did you develop your methodology?
We sought to test materials at concept and early schematic design phase, so one of the hurdles was to find an appropriate software that allowed us to do that. Once we determined what software to use, we zeroed in on the primary structure and envelope as the most impactful components to analyze and ran a base scheme of typical assemblies against low carbon versions, generating live cost comparisons for each.
We used a European software because it was the best available option for what we were hoping to achieve. Europe closely regulates how manufacturers report their environmental product data (EPD), but we don’t see the same uniformity in the data from American manufacturers whose products we regularly use. This means added extra steps to understand their EPD and sufficiently compare systems. In this situation it wasn’t as cumbersome because we only looked at two components, but with each added component it would become more challenging and onerous—a problem for design teams often constrained by time. Our experience highlighted the need for uniformity in the American manufacturers’ reporting system. It’s our responsibility to hold each other accountable if we want to make progress in reducing our carbon footprint, but we can’t do this without proper data.

What was the outcome of your study? Do you foresee applying this knowledge to future projects?
We discovered the premium for leveraging low carbon materials was not as high as we anticipated and could be offset by a variety of other factors. For example, a change in the concrete mix dramatically decreased the embodied carbon in our base scheme (by 42%), far outweighing the 2% cost premium. While small changes like this could have a big impact, the use of cross laminated timber for the primary structure demonstrated the most potential value. When combined with the material’s significance as a differentiator in the marketplace, its cost could be offset by an extra $1.50 per square foot in rent.
This experience allowed us to attribute real metrics to embodied carbon and translate those findings into terms that resonated with our client’s objectives at a pivotal point in the design process. Working alongside a client who shared our vision was vital to the process, but so was teaming with partners whose experience and prior knowledge we could lean on. These multiple perspectives combined with actual data proved invaluable in producing meaningful results.
Download the full study to learn more about the embodied carbon lifecycle analysis of 1300 Sycamore.
